In today's digital era, semiconductor technology serves as the driving force behind the innovation of electronic devices, and the pick-and-place machine, as a crucial component in this technological evolution, is quietly reshaping our lives.
Principle of Pick-and-Place Machines:
The pick-and-place machine is a highly complex and precise apparatus, with its operating principles rooted in the core of microelectronic component manufacturing. These machines utilize advanced vision systems, such as optical sensors and high-resolution cameras, to detect and position minuscule electronic components. This visual system operates with accuracy at the nanometer level, ensuring the precise placement of components.
"Pick-and place" typically refers to surface mount technology, a method of assembling surface-mount components (abbreviated as SMC/SMD, known as surface-mount devices) with no or short leads, onto the surface of a printed circuit board (PCB) or another substrate. This is accomplished through techniques like reflow soldering or wave soldering for circuit assembly.
△SMT process
In addition, "pick-and-place" also refers to the assembly technique applied to bare semiconductor dies (Die). This process involves affixing chips (bare dies) from the wafer, which lack packaging or protective layers, onto a substrate. These chips are typically made of materials like silicon and undergo processing through techniques such as etching, deposition, photolithography, and more.
△The process of die mounting
Bare die assembly is a highly precise and technologically advanced manufacturing process. In the pick-and-place procedure, the absence of protective packaging for bare dies necessitates elevated requirements for testing and assembly. Specialized pick-and-place machine equipment and techniques are essential to ensure the reliability and stability of the bare die. Bare die assembly technology is commonly employed in high-performance computing, optical communication, storage, and other application domains where increased processing power and integration are crucial.
△Differences in mounting heads for different mounting processes
Classification of Pick-and-Place Machines:
Pick-and-place machines can be categorized into various types based on factors such as their operating principles, application domains, and pick-and-place technologies.
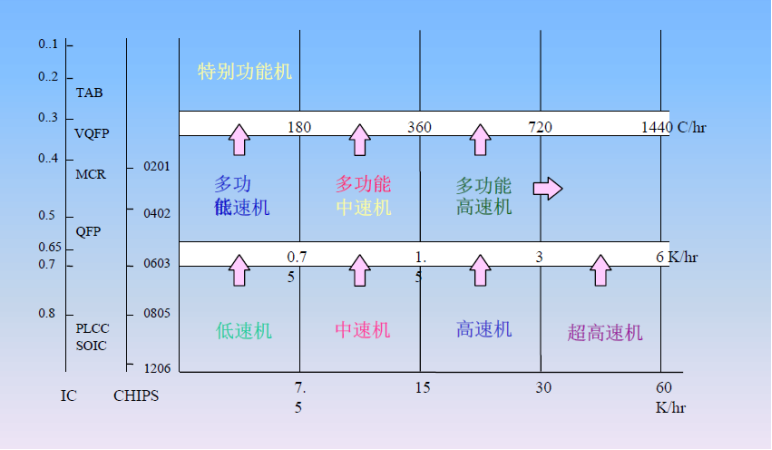
Vision-Based Pick-and-Place Machine: Relies on high-resolution cameras and image processing systems for accurate component placement through visual system precision.
Optical-Based Pick-and-Place Machine: Utilizes optical sensors to achieve component positioning through methods such as light reflection or transmission.
2. Classified by Pick-and-Place Speed:
Low-Speed Pick-and-Place Machine: Suitable for small-batch production, emphasizing accuracy over high output.
Medium-Speed Pick-and-Place Machine: Balances production efficiency and accuracy, suitable for medium-scale manufacturing.
High-Speed Pick-and-Place Machine: Characterized by high speed and efficiency, suitable for large-scale production with lower precision requirements.
3. Classified by Mechanical Structure:
Single-Station Pick-and-Place Machine: Handles one pick-and-place task at a time.
Multi-Station Pick-and-Place Machine: Equipped with multiple workstations, simultaneously performing multiple pick-and-place tasks to enhance production efficiency.
4. Classified by Automation Level:
Fully Automatic Pick-and-Place Machine: Achieves complete automation from raw material loading to component placement.
Semi-Automatic Pick-and-Place Machine: Involves manual intervention in certain steps, suitable for specific process requirements.
These classifications are not mutually exclusive; in practice, a pick-and-place machine may possess multiple features to meet diverse production needs. With ongoing technological advancements, new classifications and technologies continue to emerge, driving progress in semiconductor pick-and-place technology.
Addressing varied industry demands for efficient and precise pick-and-place technology, Bozhong Semiconductor introduces the Xingwei series fully automatic high-precision eutectic pick-and-place machine and Xingchi series high-speed, high-precision die bonding pick-and-place machine. These machines provide customers with more advanced and reliable packaging solutions across different chip and device pick-and-place scenarios.
The MicroStar series eutectic pick-and-place machine is a multifunctional chip assembly equipment known for its high precision and efficiency. With an accuracy of ±0.5-3μm, it possesses capabilities for eutectic bonding, glue dipping, and more, catering to various chip assembly needs, including COC/COS/FlipChip packaging forms. The machine features a structure design with dynamic automatic nozzle replacement (12 nozzles), multiple transfer stations (8 stations), and supports various loading methods such as blue film, Gel pack/waffle pack, track, and more. It finds extensive applications in optical communication, semiconductor packaging, laser radar, RF microwave devices, sensors, and power device packaging.
The FastStar series die bonding pick-and-place machine is a high-speed, high-precision device designed for multi-chip packaging. With a real placement accuracy of ±7μm, it is suitable for high-speed, mass industrial production of multi-chip assembly, often customized for COB packaging with tailored adhesive processes. This equipment offers customers the ultimate efficiency in on-demand customization, incorporating features such as dispensing, automatic tool changing, and hot pressing bonding. Adopting an open architecture and modular design, it provides exceptional on-demand customization capabilities, capable of handling up to 12-inch wafers and compatible with various substrate conveyance methods.
With the continuous development of technology, pick-and-place machine equipment is encountering new challenges and opportunities. In the future, as 5G technology, artificial intelligence, and the rapid growth of the Internet of Things unfold, the performance and functionality requirements for electronic device components will further escalate. This, in turn, will pose higher demands on pick-and-place technology.